
However, corrective procedures should include enough flexibility to allow quick resolution of particular non-conformities without having to make exceptions on a frequent basis. Most critical: A non-conformity requires a CAPA and resolution in a timely manner.Critical: A non-conformity requires a CAPA and resolution, but in a less timely manner.Opportunity: A non-conformity provides an opportunity for improving a product or process via a non-CAPA pathway.No action required: Applicable in cases of non-conformities that are cosmetic rather than functional problems and where the event is relatively rare, the risk relatively low, and potential solutions would be cost-prohibitive.These investigations usually lead to one of four courses of action: Leveraging the ISO 14971 risk management standard is recommended to help assess the non-conformity as well as appropriate corrective actions necessary. The initial investigation of a non-conformity should aim to understand issues including pervasiveness of the problem, the risk it poses and the likelihood if its recurrence. Initial investigations conducted in a timely manner.QMS and CAPA personnel should ensure that appropriate tie-ins exist between nonconformity and feedback forms. Manufacturers should use a non-conformity workflow and associated forms to document a nonconformity event as well as any related feedback from customers or internal sources. Documenting nonconformities and feedback.
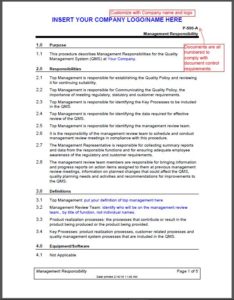
“It’s advisable to take a risk-based approach to CAPA management and allocate time according to criticality of nonconformities, while handling lower-risk items outside of a full CAPA mitigation,” says Ken Pilgrim, Senior RA/QA Consultant at Emergo by UL.
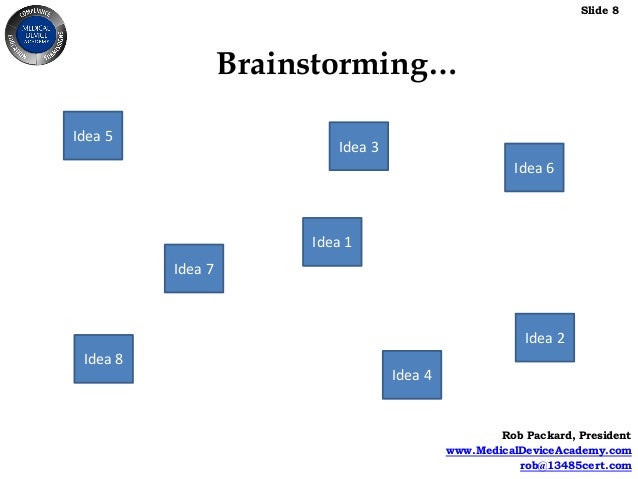
Below, we’ll discuss a roadmap applicable to manufacturers of various sizes to support effective and compliant CAPA efforts. In order to accommodate these variances, regulators allow risk-based, least-burdensome approaches to CAPA management.Ī five-tier risk assessment-minimal, low, moderate, significant or critical-feeds into three major CAPA categories (opportunity for improvement, minor or major).

However, appropriate actions often vary from company to company, as well as depend on the nature and severity of a nonconformity. Regulators typically cite “appropriate actions” as necessary for manufacturers to take in order to address nonconformities under CAPA processes. “Therefore, it is recommended to have your CAPA experts work with your product or process experts to successfully remediate an issue and develop an optimal solution.” CAPA and “appropriate actions” “The people working on CAPA processes are the most familiar with those processes, and are most likely to be able to create solutions that will work for their firms,” says Luana Zerafa, Senior RA/QA consultant at Emergo by UL. In general, companies must first ensure that employees designated to oversee CAPA processes are properly enabled and empowered to do so. However, effective CAPA management can prove a perennial challenge even to larger, more mature manufacturers.Įmergo by UL consultants with expertise in medical device quality management system implementation and training have identified several processes and steps to help manufacturers establish and maintain compliant CAPA practices that are also scaled appropriately for their operations. Ensuring adequate processes for corrective and preventative action (CAPA) management is a critical step for medical device manufacturers implementing ISO 13485:2016 or other quality management systems.
